Portfolio
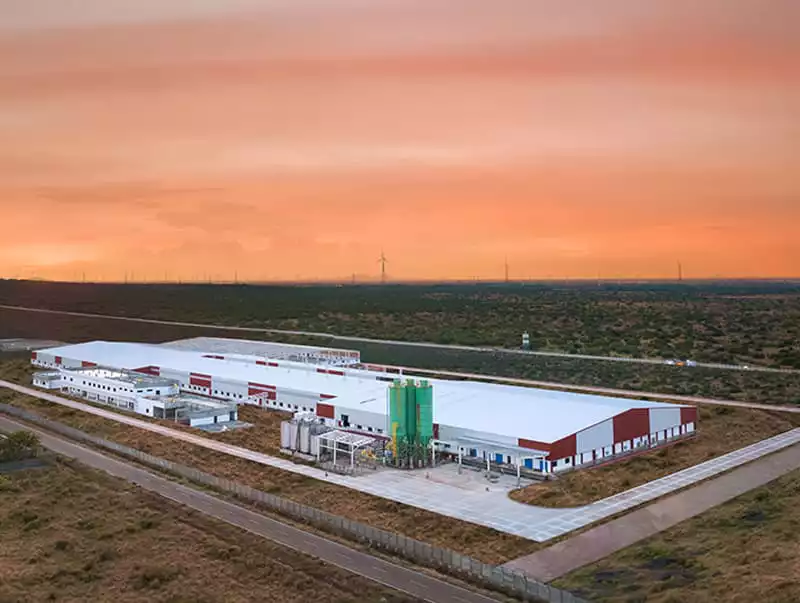
The Britannia factory located in Tamil Nadu required the right amount of ventilation for maintaining suitable moisture content and temperature for the finished goods. Double Skinned roofing with mineral wool insulation was used to meet temperature requirements. Openings were provided carefully for controlled air circulation with a combination of louvers and roof monitors. The building required many chimney openings for operational necessities, which in turn made roof sheeting more challenging. By using specially designed Metal Roof Curbs the team was able to meet the requirements of the client and ensure leakproof and watertight functionality of the building.
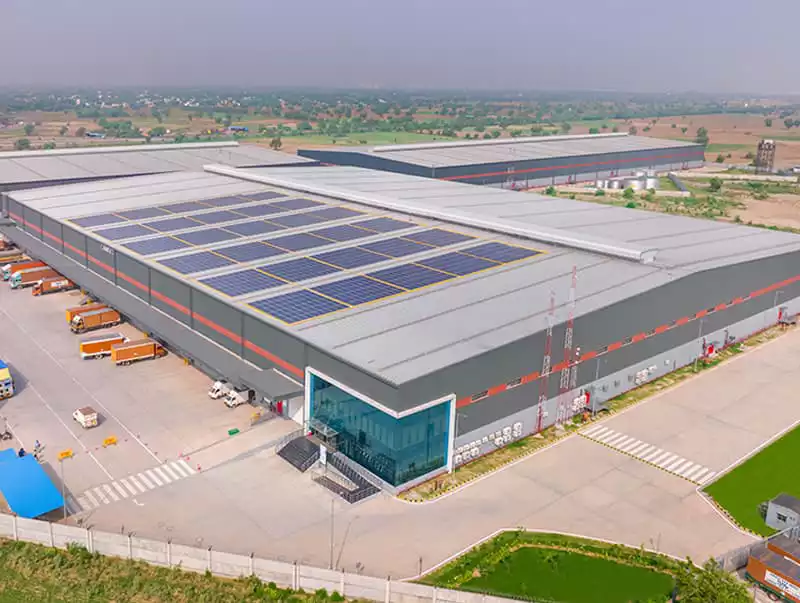
The Built-to-Suit EMS-3 (multi Span 3) warehouse building has an office mezzanine floor. XLPE Insulation was provided for maintaining ambient temperatures. Reverse canopies were provided for aesthetic appearance. The harsh weather at the site damaged the roll-forming machines which delayed the roof sheet laying. An alternate machine was shipped to the site immediately and continued the work.
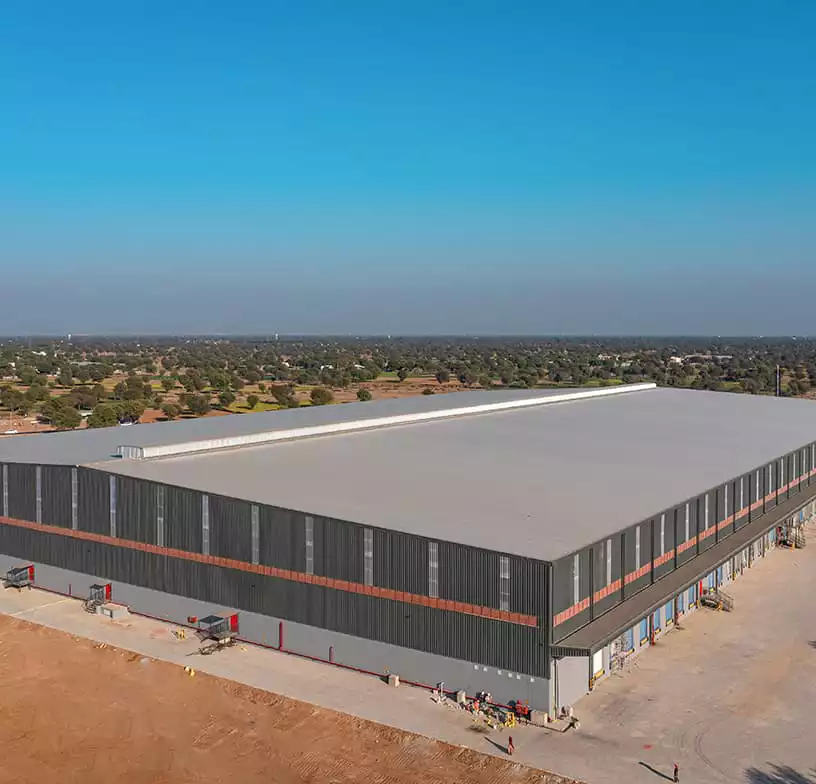
The Warehouse has an area of over 3.5 lakh sq. ft. Everest designed a multi-span frame with optimum column spacing to achieve the layout requirements. Jack Portals and Jack beams were provided to reduce interior columns for unhindered space required for material movement inside the building. Everest used the latest SS470 standing since the customer was very concerned with water leakage. The building has future expansion at the end wall which called for careful designing of the end wall columns and secondary systems, including wall cladding since the customer wanted wall cladding and columns to be removed to pave way for expansion. Everest accurately planned for the material dispatch to follow the erection sequence.
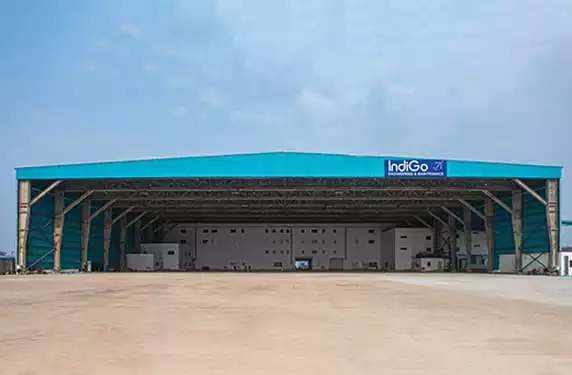
The end user, Indigo, and the consultant had specific limitations of floor area usage strictly imposed by the authorities that were making the design of the airplane hangar impossible by conventional methods. By using a pinned base, the area of the base plate was reduced by nearly 70% and an overall saving of 10% was realized in the weight, thus pioneering the implementation of this concept as per customer requirements.
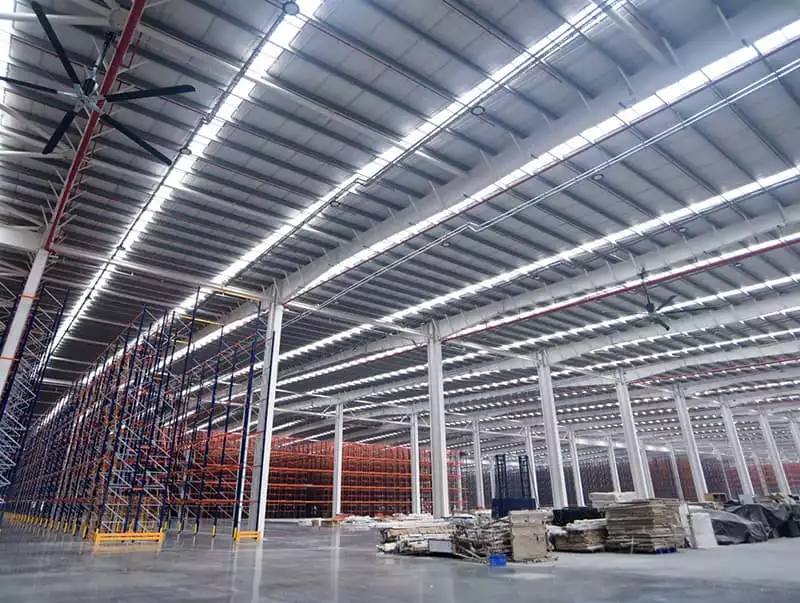
To cater to the client’s need for a single 80 m roofing profile to minimize leakage risk, Everest erection did complete site roll forming of the roofing profile, and an 80 m long roof sheet for the warehouse building roof was successfully profiled at the site.
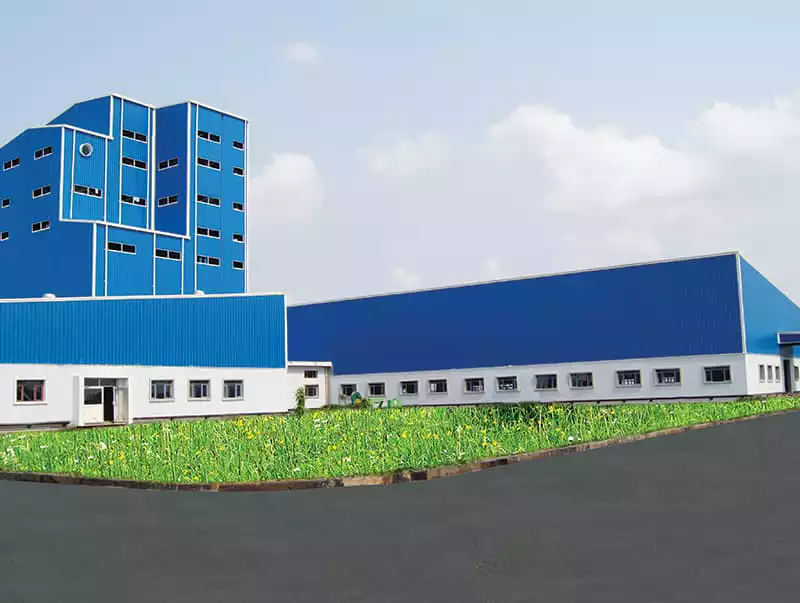
To address the increasing requirement for edible oil, Godrej Agrovet Ltd. proposed to construct a Greenfield facility near the palm oil field in Chintapalli Mandal, Andhra Pradesh. In order to complete the project in a timely manner, Everest developed solutions to conduct the entire installation of the building from outside using cranes. For this purpose, two 180 MT cranes were used to complete the erection work on time. The material was lifted to a height of 40 m to complete the boiler house building. Prior to the commencement of any construction activities, a safety briefing was conducted for all personnel onsite to safeguard the health & safety of workers. Everest Industries Ltd delivered a very complex 34.8 m high G+6 multi-story process plant for Godrej Agrovet under difficult site conditions with full compliance with safety.
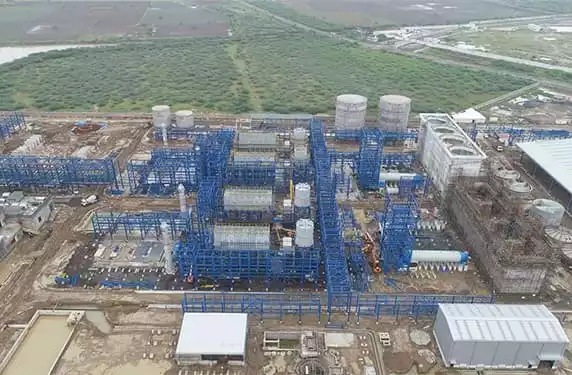
Everest's crew of veteran designers and detailers teamed up with CTCI's unit in Taiwan to transform their design into a local dialect for finding material sourcing. The structures were subdivided into five sections in accordance with the priority and also for sufficient materials to be obtained. To ensure that the inspection clearance process does not delay production, a joint committee of quality personnel from both Everest & Cinda was put in place to be available on-site at all times.
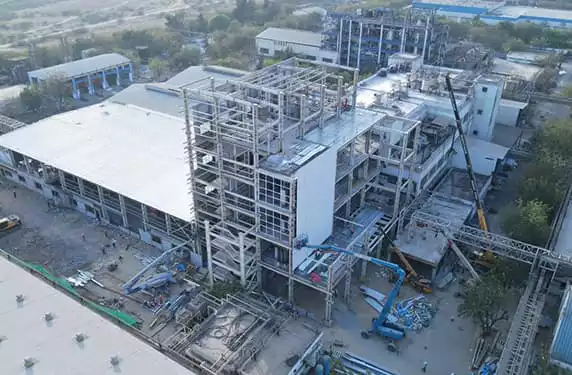
Owing to the demand in the western part of the country, Lakme lever urgently needed to expand their Gandhi Nagar unit. Since the factory premise has space constraints & processes at the proposed unit needed to have a connection with the existing unit, a space adjoining the existing plant was identified. This brownfield construction of the proposed building involved the design, manufacturing & erection of a 28-meter tall structure at a severe seismic zone (zone V). Everest was entrusted to execute the complex factory building. The design was done on TEKLA software to have error-free output. Erection was carried out in multiple shifts to meet the challenging timelines of 3 months.
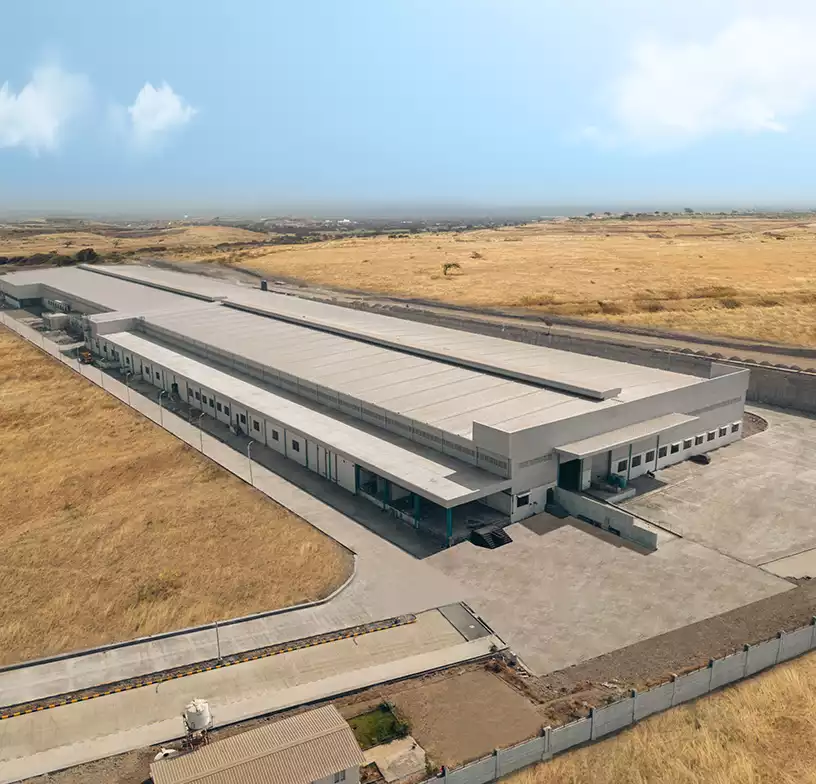
The layout of the IFB building was planned by Everest in such a way that there was maximum unobstructed space for material and people movement. The building had critical height requirements with respect to Lean-To and EOT cranes and spans more than 350 meters in length, which makes the building susceptible to temperature effects and stresses during temperature variance.